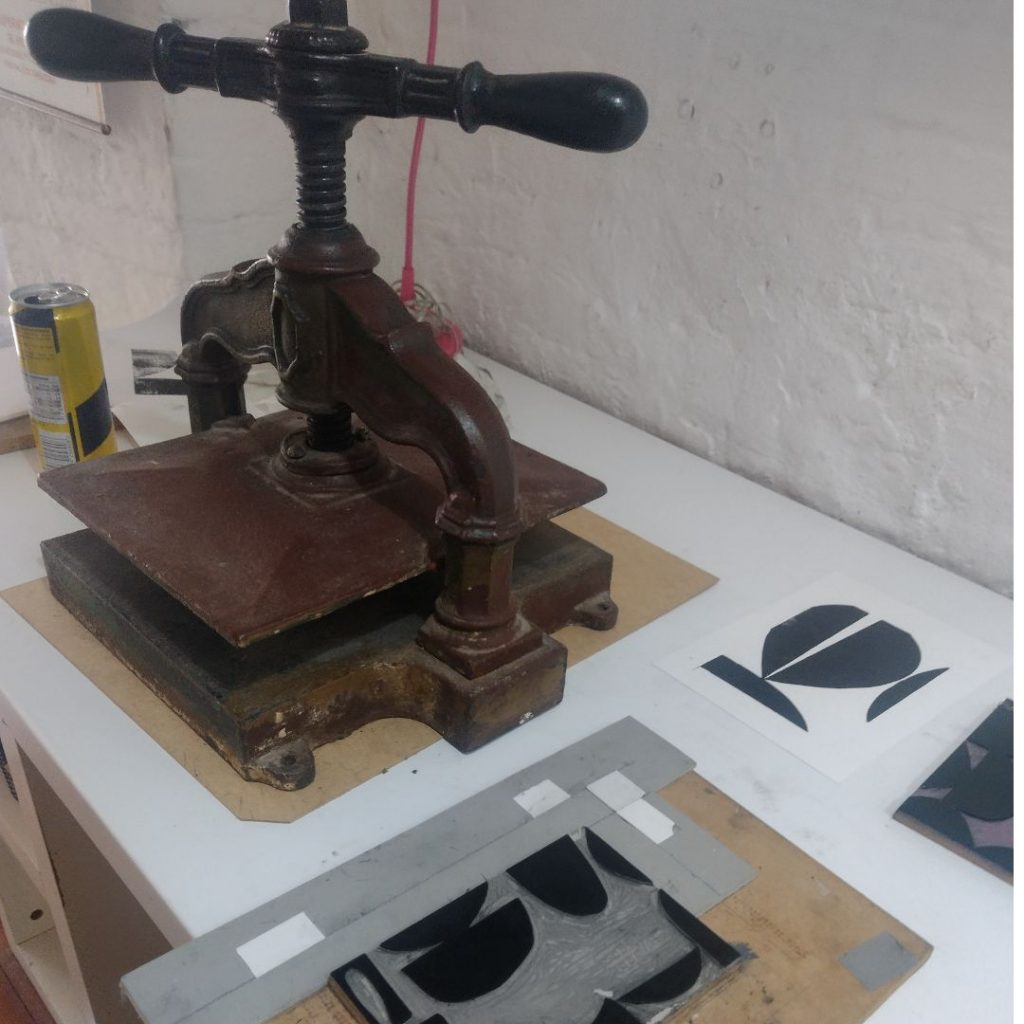
Here is my Victorian Cast Iron Book Press is a heavy, durable device used in the 19th century, primarily for pressing books during the binding process. It’s made entirely of cast iron and features, flat pressing surface with a screw mechanism on top. The press operates by turning a wheel or handle attached to a central screw, which lowers a flat, heavy platen (the pressing surface) onto the material below. The cast iron construction allows for the generation of significant pressure, essential for the tasks it was designed for, such as bookbinding, flattening paper, and other similar processes.
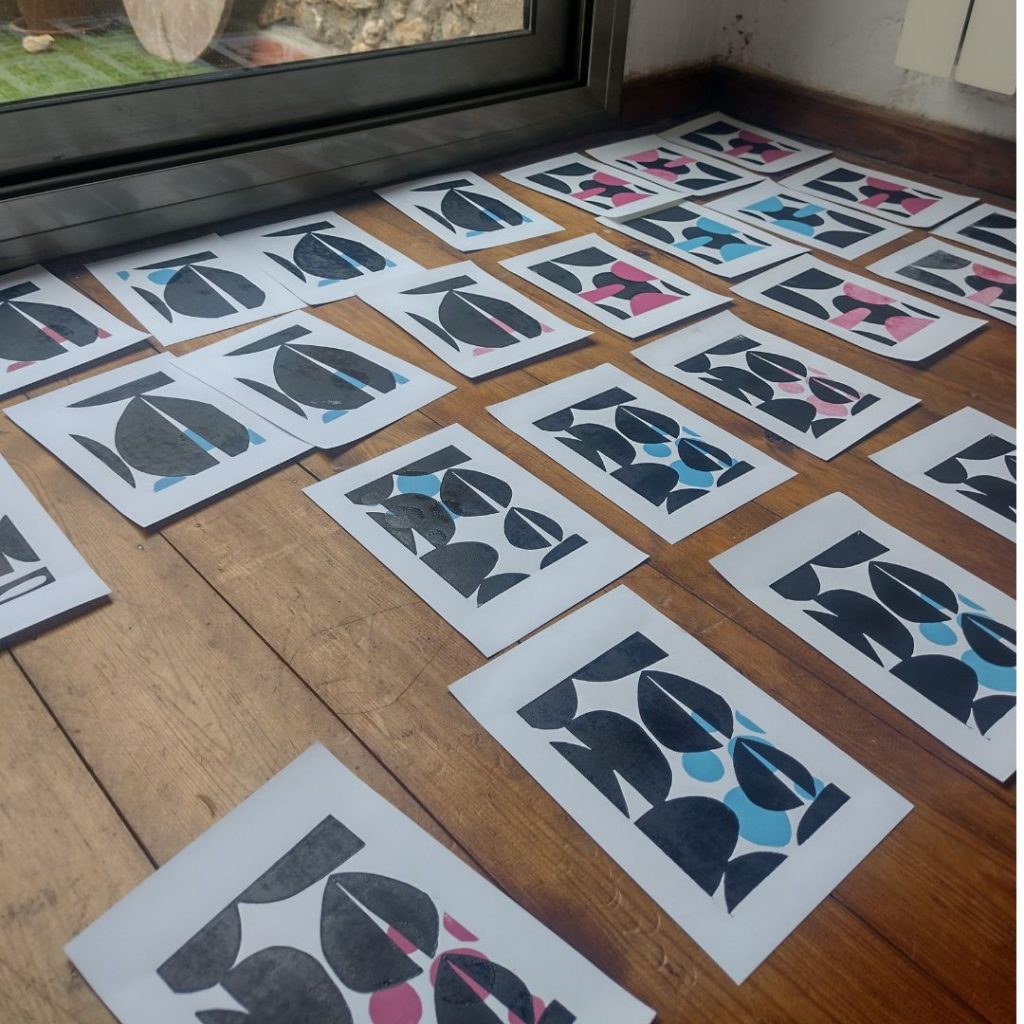
Usage in Lino Printmaking:
In lino printmaking, a linoleum block is carved to create a design, which is then inked and pressed onto paper to produce a print. While a hand brayer or dedicated printing press is often used, a Victorian Cast Iron Book Press can serve as an effective alternative.
Inking the Block: First, the carved linoleum block is evenly coated with ink using a a roller.
Positioning: The inked block is then placed on the platen of the book press, with a sheet of paper laid on top then coverd with a blanket.
Pressing: The upper platen of the book press is lowered onto the paper and block by turning the screw mechanism. The heavy cast iron construction allows for even and consistent pressure, crucial for transferring the ink from the linoleum block to the paper.
Final Print: After applying the desired amount of pressure for a sufficient amount of time, the press is opened, and the paper is carefully removed to reveal the printed design.
Using a Victorian Cast Iron Book Press in lino printmaking provides a unique, hands-on method of creating prints, harnessing the weight and precision of the press to achieve a clean, even print with good ink transfer. The process is slower and more manual than using a modern printing press but offers a satisfying connection to historical printing methods.